- ·上一篇文章:模具斜导柱长度的算法
- ·下一篇文章:典型机床夹具—铣床夹具的分类
航空发动机压气机叶片工装标准化
一.前言
我公司是从事航空发动机压气机叶片(以下简称叶片)精密锻造和机械加工的专业厂家,产品工艺主要特点是:叶身、缘板无余量精锻,机械加工叶片的安装等部位。这过程中,几乎各个工序都要使用专用工装来加工和检测,工装设计的合、工装制造的精度直接决定能否研制出合格的叶片。
叶片工装种类多,数量大,空间角度多,设计制造技术难度大,周期长,常常不能满足研制周期的要求,大量工装现场存放管理费时费力。为缓解这些压力,我们适时对叶片工装进行了大量的标准化工作,明显提高了设计效率,缩短了制造周期。
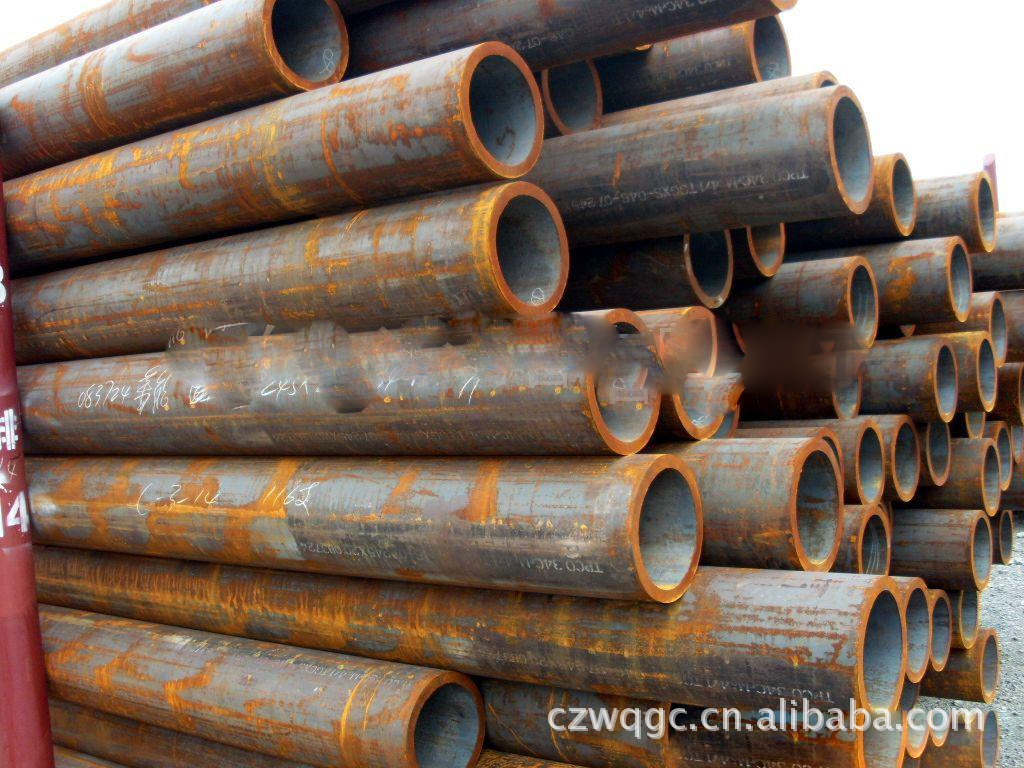
二.工装结构的标准化
完成某一工艺功能的叶片工装往往有多种常用典型结构,仔细分析它们的共性、个性、各方面优缺点,找出规律性,综合工艺及现场操作人员的意见,依据标准化原则,视不同情况将结构进行简化、统一化、系列化、通用化、组合化。
叶片的形状不规则性导致工装多数采用空间点、型线或型面来定位夹紧,这部分尺寸、结构变化较大,要完全标准化不太现实;但除此之外的其它零部件结构却有很多共性,经过对比筛选,可找出一般规律将它们不同程度的标准化。我们对预终锻模、切边/叶尖模、进排气边铣削夹具、浇铸夹具、榫头铣削/拉削/磨削夹具、锻造缘板高度测具、榫头三坐标测具、投影测具、叶根最大轮廓过规、叶尖长度测具等工装进行了标准化,下面将就一些实例具体介绍。
图1转子叶片浇铸夹具
2.1浇铸夹具的标准化
首先,统一结构。浇铸夹具有立式、卧式两种结构,由于立式结构体积较大,密封效果不太好,操作也不太方便,而卧式结构则相对较好,产品质量也较稳定,最终把卧式结构的浇铸夹具确定为标准结构。见图1所示。
图2浇铸夹具底座
其次,简化结构。将这种结构拆分为三部分:底座部分,
完成传动夹紧功能,见图2;主体部分,实现定位及成型浇铸块功能,见图3;浇铸块部分,实现与其它工装关联,见图4。拆分后,原来复杂的结构衍变为相对简单的三个子模块。
图4浇铸块
接下来系列化浇铸块外形尺寸。主要是指转子叶片,而静子叶片一般是采用车削工艺,用车床软爪直接夹持,不用过多考虑它的大小。以前,几乎每个叶片都有独特尺寸的浇铸块,存在很多弊端。通过对叶片锻造毛坯尺寸分析分类,简化其结构,基本确定为图4结构,最终确定了三种外形截面尺寸系列:30cmx45cm;50cmx70cm;70cmx100cm。其适用于公司目前所有的转子叶片。这样做的优点将在下述及下一节2)中体现出来。
图5静子叶片浇铸夹具
最后,通用底座。转子叶片浇铸夹具(见图2)、静子叶片浇铸夹具(见图5)有各自的结构特点,仔细研究后发现它们的底座结构都差不太多,仅导轨行程差别比较大,完全可以通用化。经过综合,重新设计通用底座(见图6),冲压毕业设计。在这个结构中增加了调整块(件6件7)以适应浇铸块的三种系列。
图6浇铸夹具通用底座
底座通用,浇铸块系列化风扇叶片(2),在新叶片设计中,将采取组合化设计,根据叶片大小先确定一种浇铸块系列,再设计主体(专用)部分即可,设计工作量能减少三分之一,制造工作量能减少五分之二。
浇铸夹具是叶片机加工艺中最重要的一项工装,涉及面广,结构复杂,设计制造难度大。我们最早从其着手,综合运用了简化、统一化、系列化、通用化、组合化等方法,对浇铸夹具进行标准化,取得了非常好的效果。
2.2浇铸块周边工装的标准化
由于浇铸块尺寸的系列化,给与浇铸块相关的工装标准化系列化带来可能,如铣榫头夹具、拉榫头夹具、带浇铸块三坐标检榫头测具、带浇铸块投影测具等。
标准化方法很简单,针对三种系列浇铸块尺寸,分别设计与其尺寸相对应的三种系列标准工装。选用方法:当新的项目启动后,根据叶片形状,先确定浇铸块系列型号,小型冲孔弯曲件冲压模设计。再从上述四种测、夹具中选出与浇铸块相对应的型号,使用者根据型号从库房中领取。
以30cmx45cm浇铸块为例进行说明。
图7为铣削夹具,一般情况可通用。
夹具设计手册图8通用三坐标测榫头和投影测具
图8为一测具,同时具有带浇铸块三坐标检榫头和投影两种功能。对于使用三坐标检榫头,一般情况可通用;对于投影,如果只投影榫齿方向,则一般情况可通用,如果还要投影端面方向,仅需临时设计制造一个专用角度块,连接到底板上即可。